Connecting Flanges: 10 Common Mistakes and How to Avoid Them
By KLINGER GPI | 5/30/2024
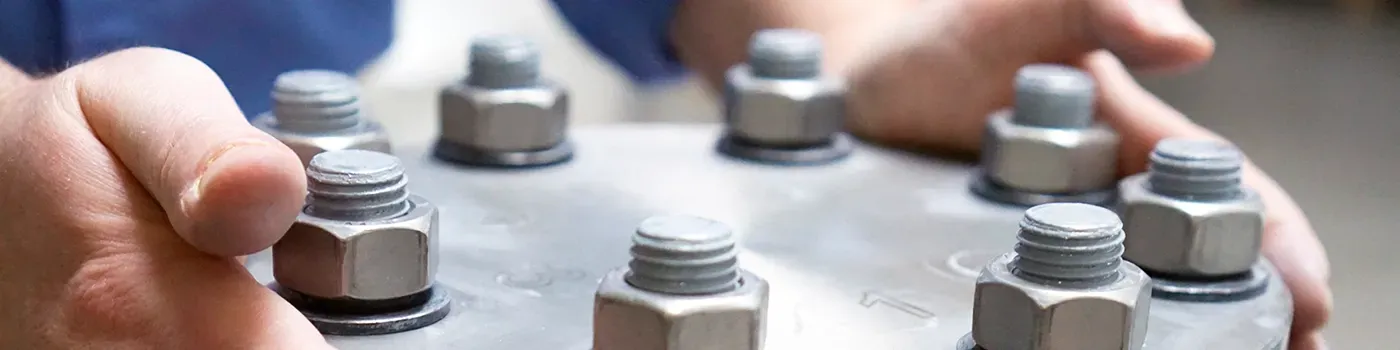
Learn the correct methods for making flange connections and avoid common mistakes with bolts and gaskets.
In this how-to article, you will get to know the correct techniques for assembling flanges and learn about common mistakes made in selecting and using gasket materials, bolts and other components.
#1 Gasket material
The gasket material plays a major role in ensuring reliable, leak-tight flange connections. A common mistake is to use unsuitable material.
WRONG: Using an unsuitable gasket material, e.g. a fiber-reinforced material for applications with liquid oxygen (fire hazard!). Reusing an already used gasket. Using a gasket that is too large or fitting the gasket off-center, so that it protrudes into the pipe.
CORRECT: Select a suitable gasket material for the application and the conveyed medium. Always fit a new gasket.
- Before you start, select the right gasket material for the task by calling your local KLINGER GPI representative.
- Discard all used gaskets. Fit a new gasket even when only servicing a valve. A used gasket will no longer give an even seal, and turning the gasket over can also cause problems.
- If the gasket is too large, parts of it can be eroded by the medium.
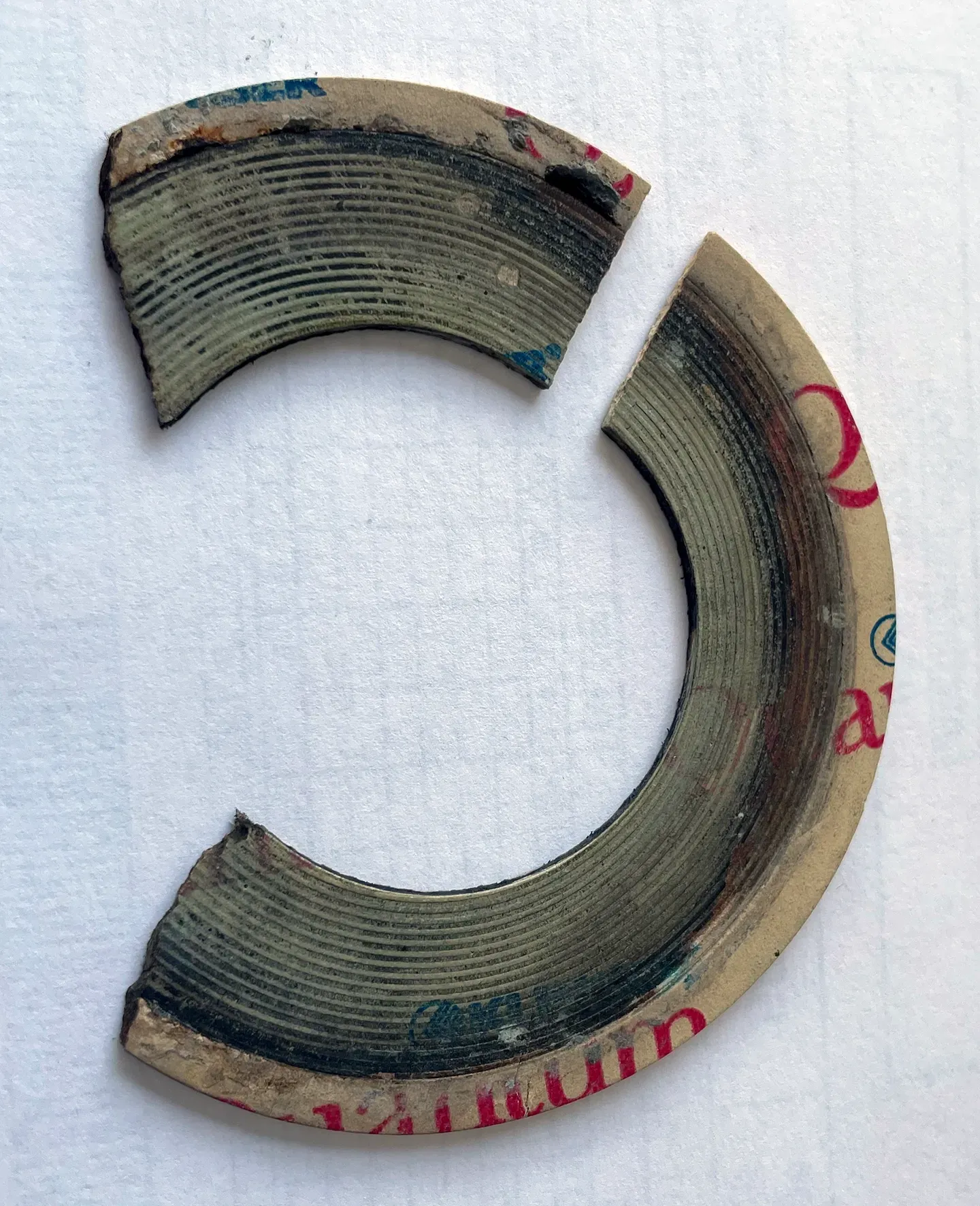
#2 Selecting bolts
Choosing the right bolts is vital to ensure the stability and tightness of flange connections. Unsuitable bolts can cause the connection to weaken.
WRONG: Using bolts other than those specified in the applicable standard. Using a different bolt material: bolts that just happen to be lying around do not necessarily match the flange material (e.g. stainless steel bolts on a steel flange). Not using washers. Mixing different bolts or using ones that are rusty or too small.
CORRECT: Use bolts, nuts and washers of the correct type, size and material as specified in the relevant standard.
- The number of bolts to use with each flange is standardized and depends on the flange size and pressure.
- Example: A flange of DN100 PN40 requires 8 bolts with an M20 thread. The standard applicable here is EN 1091-1 or DIN 2572.
#3 Opening the flange connection
Correct opening of the flange connection is crucial for safety during maintenance work. An incorrect procedure can lead to dangerous situations.
WRONG: Undoing the bolts closest to your own body first and removing them immediately. Undoing the bolts one after the other going round in a circle.
CORRECT: When undoing bolts, always start on the side furthest away from your body. Undo the bolts a bit at a time, always releasing diagonally opposing bolt pairs. With the nuts still in position, check whether the flange can be moved.
- Safety first: If the pipe still contains a medium or is still pressurized, the medium will escape. When you undo the bolts furthest away from your body first, the medium will escape away from your body.
- If the bolts are removed entirely, any tension in the pipework can cause the pipe to move towards you and cause injuries.
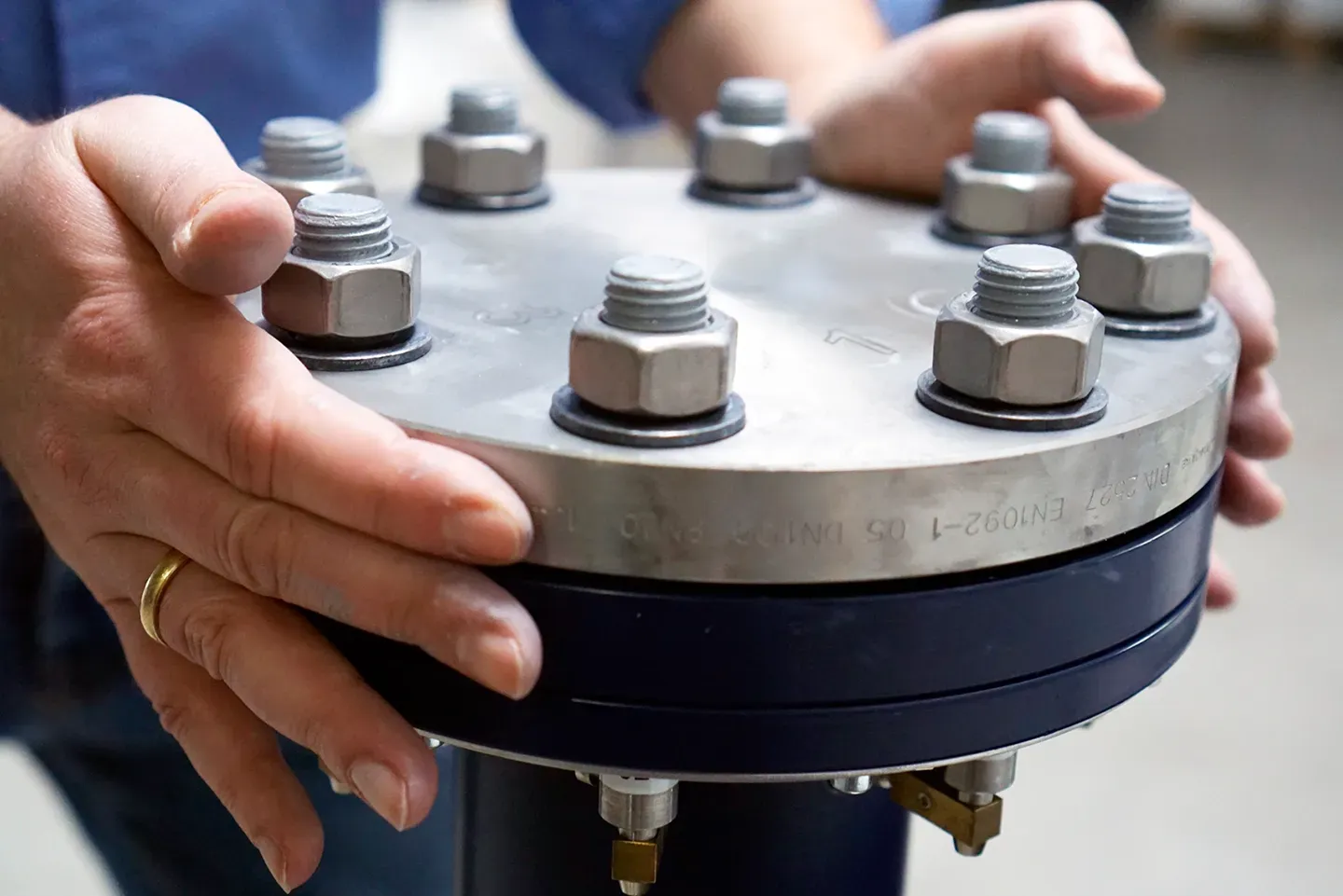
#4 Removing the gasket
When peeling off the gasket, take care to avoid damaging the flange surface, as this can cause leakage.
WRONG: Removing the gasket from the flange using a spatula. Undoing all bolts and opening the flange connection immediately.
CORRECT: Leave the nuts and bolts on the flange connection. Move the flanges slightly to ensure that the gasket does not adhere. Clean the flange with a brass wire brush. The grooves in the flange’s mating surface are visible on the gasket.
- Spatulas are usually as hard as or even harder than the flange material. They can cause scratches in the flange or rust to form, and this may result in leakage.
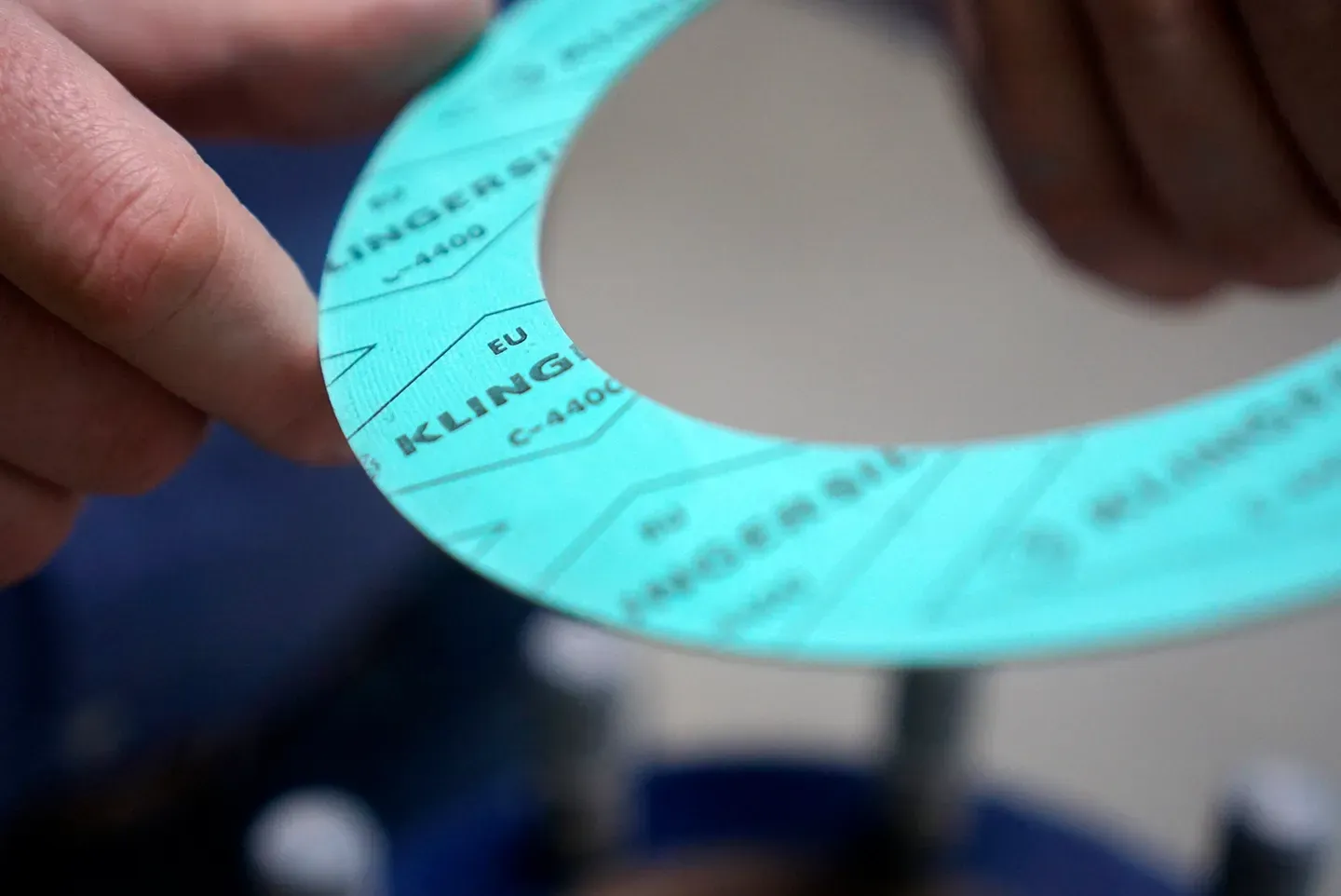
#5 Lubricating the bolts
Lubricating the bolts is important to ensure that the forces are evenly distributed and to facilitate assembly.
WRONG: Not lubricating the bolts.
CORRECT: Apply the specified lubricant to the bolts around their entire circumference. Also, apply lubricant between the nut and the washer.
- The lubricant to use is also specified in the shop papers.
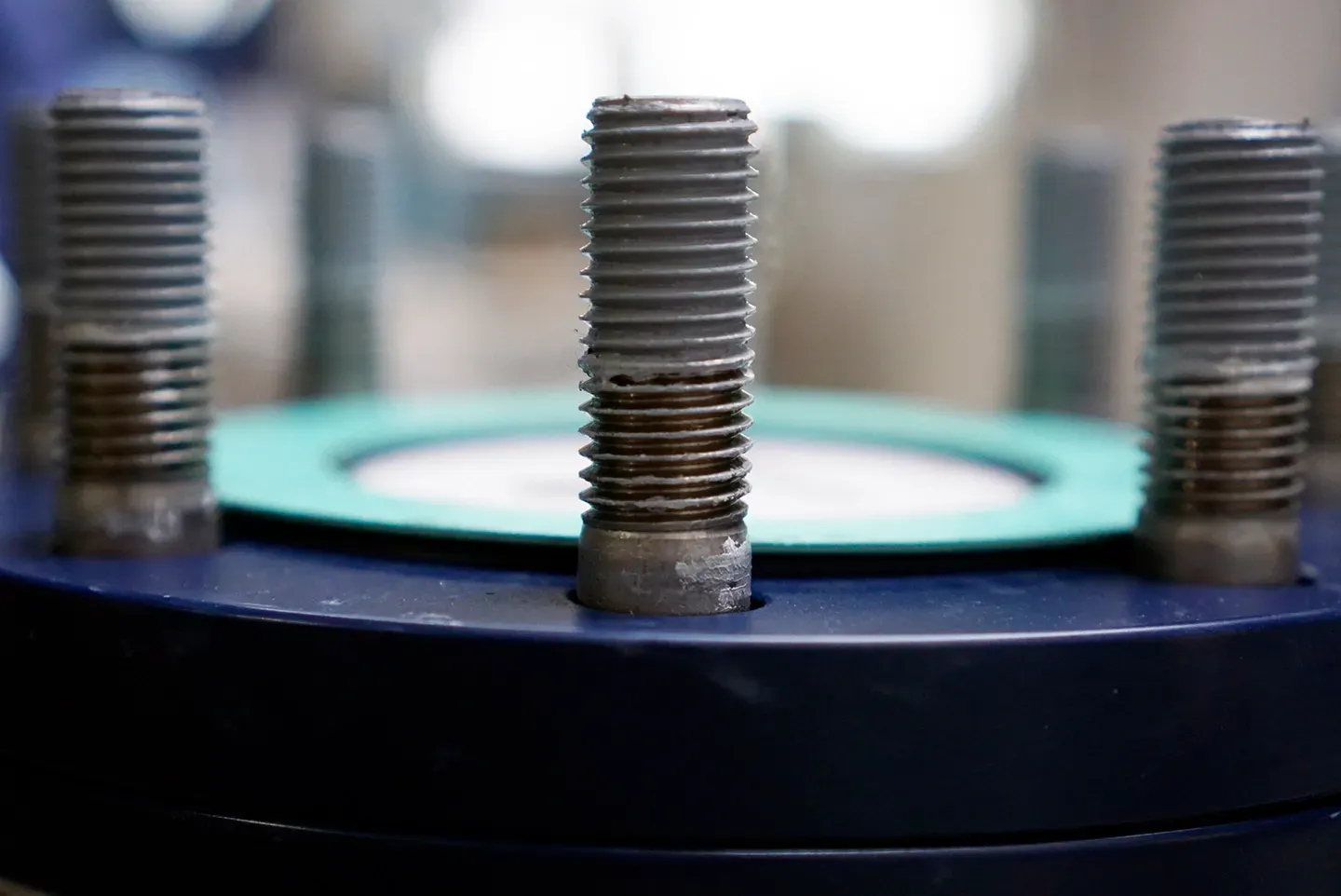
#6 Assembling the flange
Correct assembly of flanges, especially in vertical applications, is vital to ensure that the connection is stable and tight.
WRONG: Tightening the bolts on a flange in a vertical application by going round in a circle. Securing the gasket between the flange surfaces using adhesive or double-sided adhesive tape. This can lead to problems during operation.
CORRECT: For vertical pipework, first fit threaded bolts or centering bolts to the underside to ensure that the gasket does not slip through.
- For full-faced flanges: The gasket covers the entire flange surface and already contains holes for the bolts.
- For raised-face flanges: The sealing surface is slightly higher than the rest of the flange surface. This is the most common flange type.
#7 Positioning the gasket
Positioning the gasket correctly is essential to ensure that the flange connection works as intended. Incorrect positioning can cause leakage.
WRONG: Positioning the gasket at an angle so it protrudes beyond the flange or into the pipe.
CORRECT: Always center the gasket on the flange surface. When the flange is opened, the imprints of the flange grooves on the gasket are even all the way around.
- With set bolts, the gasket cannot slip. When using shoulder bolts, however, the use of centering bolts is recommended.
- The gasket can be glued on with a small drop of adhesive so that it does not slide out of position in a vertical installation. A better option is to fit bolts to the underside of the flange to prevent the gaskets from slipping out.
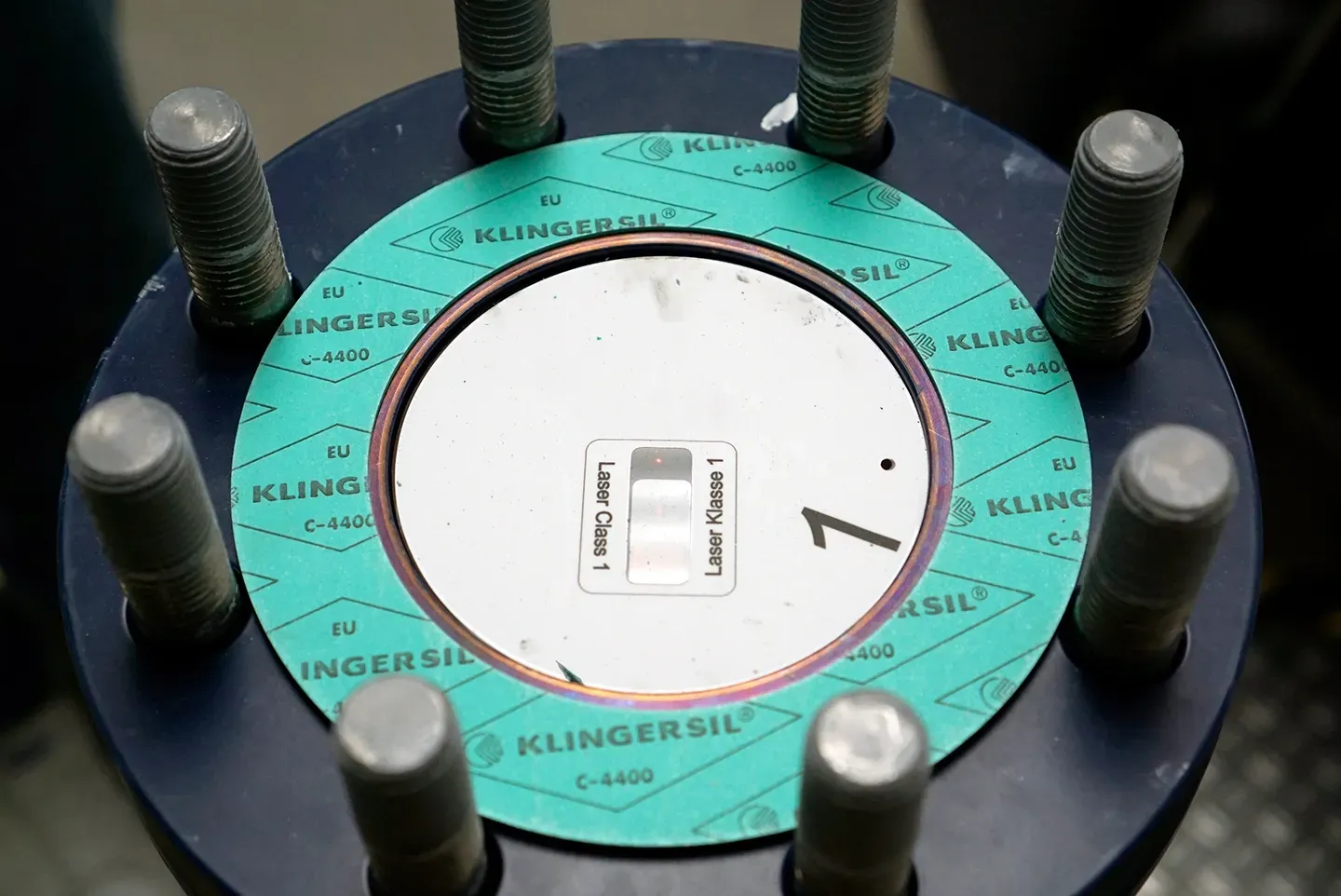
#8 Nuts and bolts
Using the correct combination of nuts and bolts is important to ensure the integrity of the connection and to avoid problems when re-tightening.
WRONG: Separating the nuts and bolts when opening a flange connection, so that the nuts and bolts are later refitted in different combinations.
CORRECT: Keep each nut-and-bolt pair together after disassembly. When reassembling the flange, refit each nut to the bolt to which it was originally fitted.
- A precise fit between the nut and bolt is vital so the flange connection has the required tension and strength. The thread and tolerance of each nut and bolt is slightly different, so it is important to match nuts and bolts correctly.
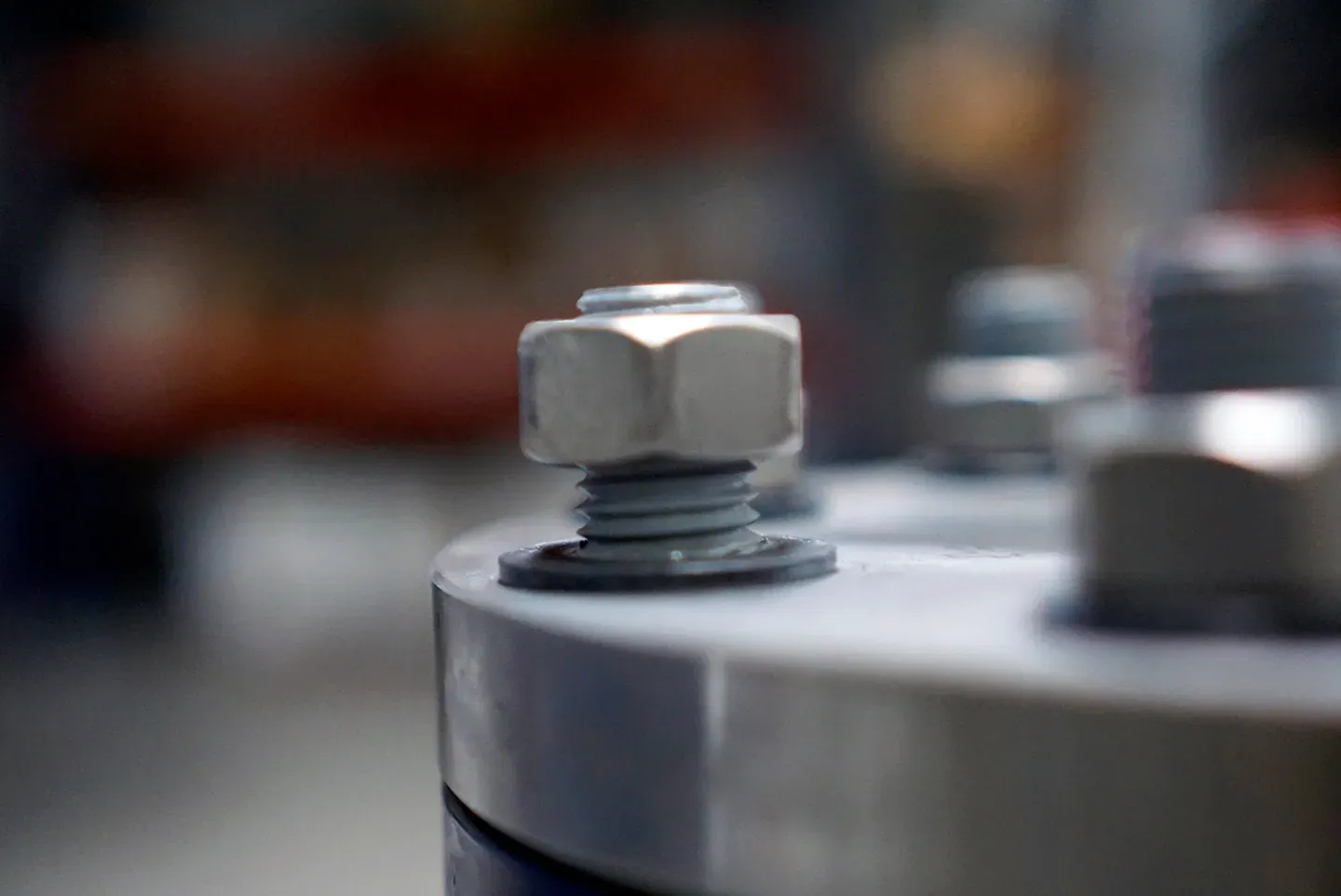
#9 Torque spanner
The correct use of tools plays an important role in precisely controlling the necessary tightening torque. This ensures an even load distribution.
WRONG: Using an open-end or ring spanner and tightening the bolts using random force. This can lead to the mating pressure to be spread unevenly over the flange and gasket, which can damage the connection.
CORRECT: Use a calibrated torque spanner to ensure that all of the bolts are tightened to the same, correct torque. Tighten the bolts in several stages, working in a crosswise pattern. Finally, tighten each bolt again to the same torque, working in a circle around the flange. This ensures that all bolts are equally tight and none have been missed.
- Using a torque spanner ensures that the bolt forces are evenly spread across the whole flange. This is particularly important, as uneven forces can cause damage to the gasket or even the whole flange connection.
- Example: If you apply 200 kN, this corresponds to a mass of 20 metric tons. This means that the flanges exert a pressure of 20 tons on the gasket. That is why it is important that these forces are spread evenly.
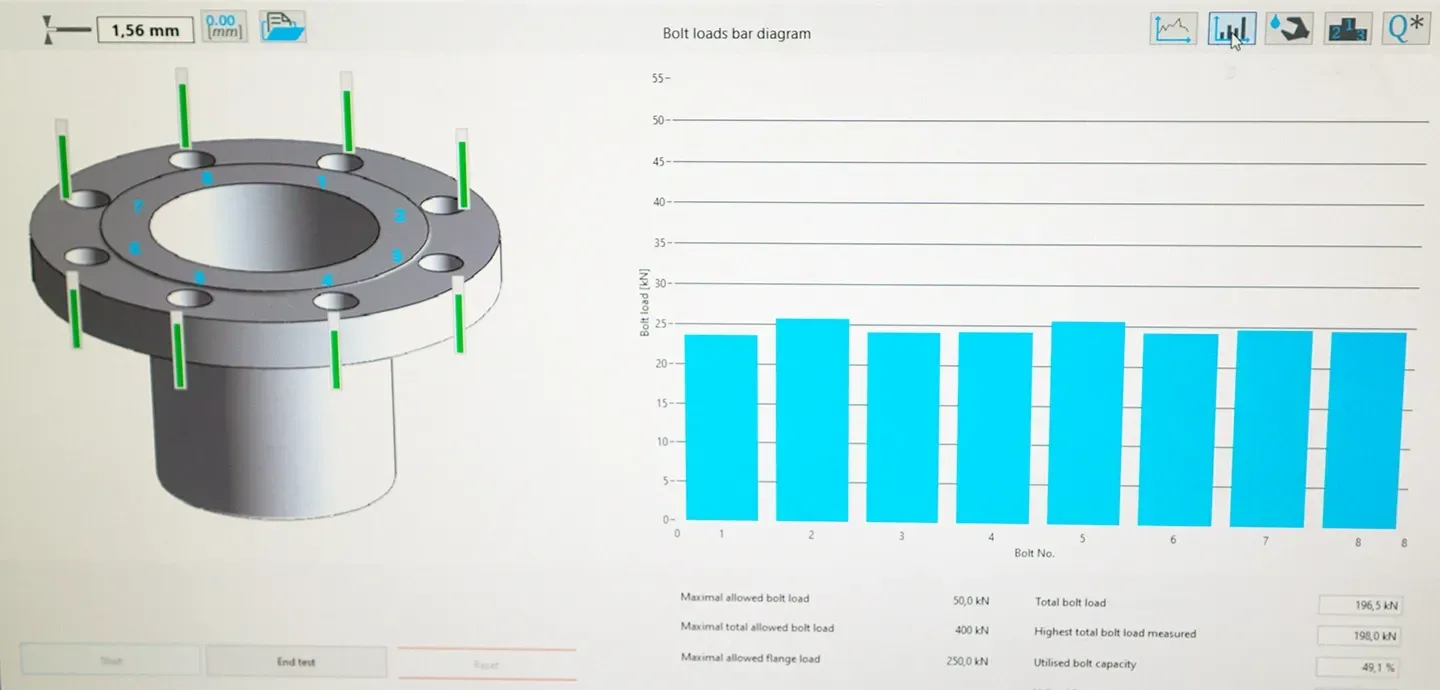
#10 Tightening the bolts
Tightening nuts and bolts in the correct order and to the correct torque is critical in the assembly of flange connections. It ensures an even load distribution and the structural integrity of the joint. Errors in this step can lead to considerable problems and safety risks.
WRONG: Tightening nuts and bolts to the full torque going around the flange in a circle. This causes an excessive load on the first bolt and may result in others remaining insufficiently tightened. The gap between the flange halves may then be uneven and the first bolt could even break under the load.
CORRECT: First tighten the nuts and bolts finger-tight. Then tighten them in a crosswise pattern in several stages, each time gradually increasing the torque. This ensures that the load on all bolts remains even and prevents the flange from tilting.
- Crosswise tightening of the bolts ensures that their forces are evenly distributed on the flange and gasket. This is vital to prevent damage to the gasket, flange and bolts.
- Tightening a bolt to its limit can easily cause it to rupture. Tightening in a circle without first finger-tightening can result in the entire tightening force being required for the first half of the flange to straighten the flange again.
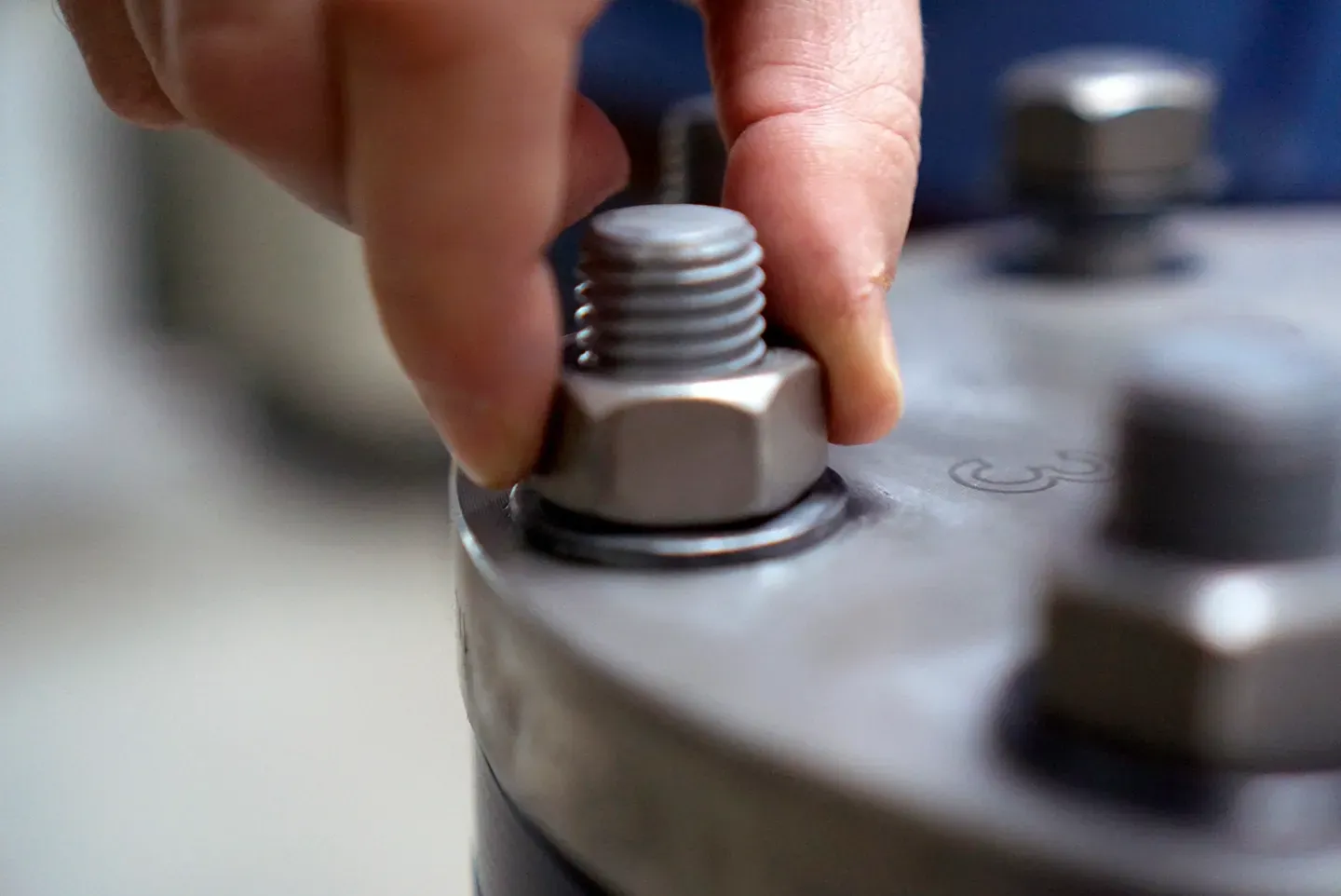
A comparison
In this example, the bolts were tightened once in a circle moving around the flange (image A, WRONG) and once in a crosswise pattern (image B, CORRECT). The forces acting on each bolt and the gasket thickness were measured in each case. A torque spanner was used in both cases.
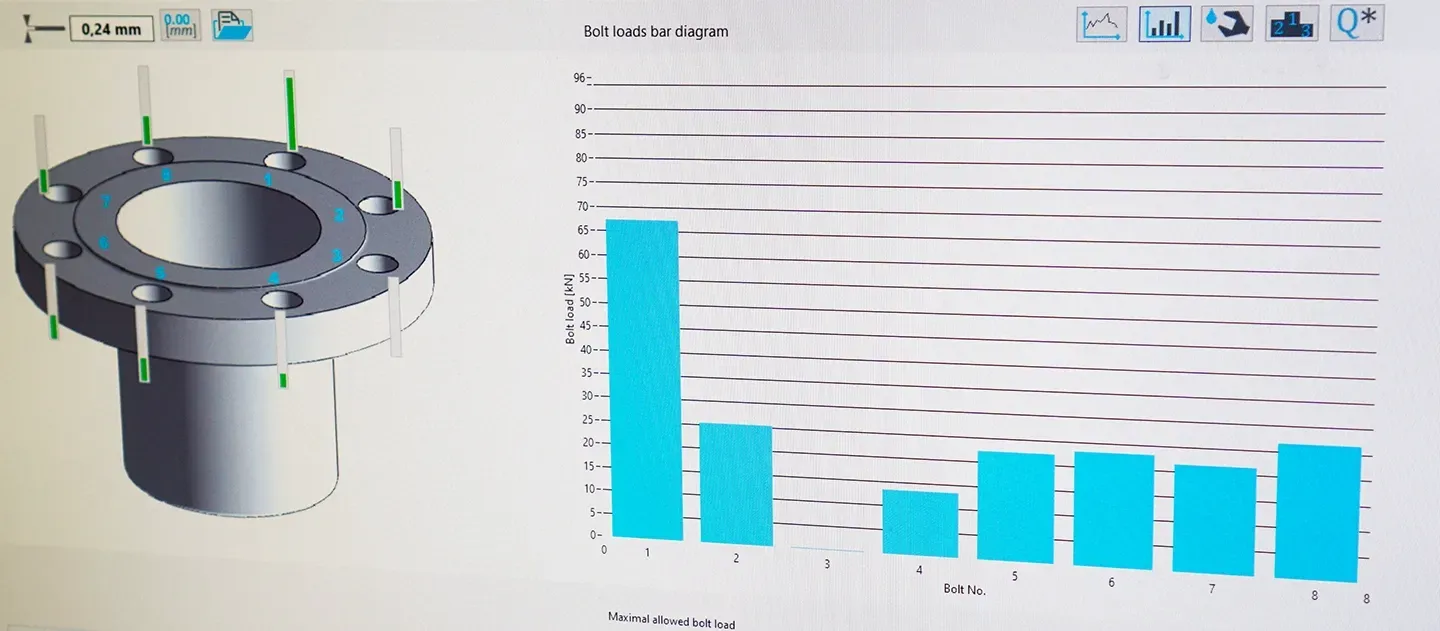
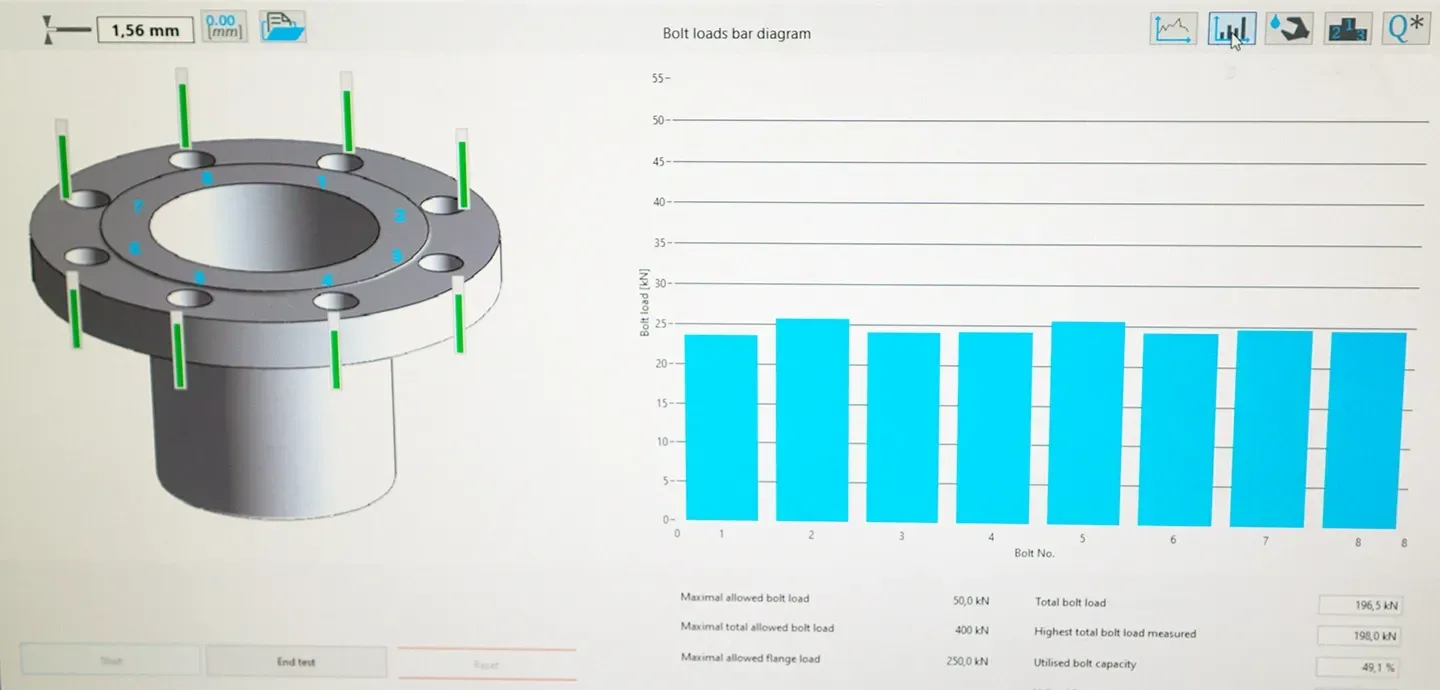
Please note: This blog post does not guarantee a leak-free installation. This how-to article explains the ten most common mistakes and misconceptions when assembling flange connections with gaskets. If you have any questions, please get in touch with your contact person.